It’s simple, Employers in BC are responsible to provide first aid in the workplace. Hire a first aider, or train an existing employee to carry out first aid duties, buy some equipment, and you’re done right? But what about those instances where the workplace is remote, or work sites where there are dozens or even hundreds of employees?
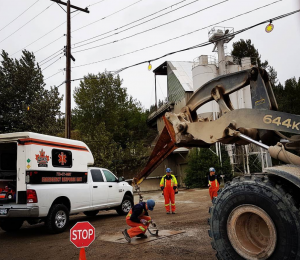
One of our mobile treatment centers with an experienced level 3 first aid attendant standing by to ensure the safely of this work-crew.
In these instances you may be required to bolster your levels of first aid to be in compliance with the Occupational Health and Safety Regulations.
To determine levels of first aid coverage, the employer must conduct a first aid assessment. First aid coverage depends on the total workforce present at each workplace and the hazard rating given to your type of work. Hazard ratings can be determined in the table found in part 3.16 of the BC Occupational Health and Safety Guidelines.
The number of workers and hazard rating are just two of the pieces you need to determine your first aid coverage requirements. The third piece is your work site’s surface travel time to hospital. After all, the survival of an injured worker depends greatly upon how quickly your first aid attendant can respond and how soon you can transport the patient to medical aid if required.
As you conduct your first aid assessment you may find that you are required to have emergency vehicles and equipment at your work site. This is where OH&S Safety Consulting and Training Solutions LTD. can help. We have fully stocked mobile treatment centers, Emergency transportation vehicles, and industrial ambulances to assist you in meeting your first aid requirements. We also provide qualified, competent, first aiders and industrial paramedics for the duration of your project.
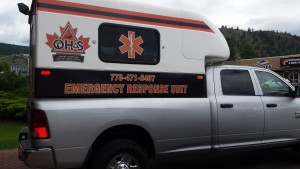
Our mobile treatment centers and first aid attendants are always ready for your project big or small
If your first aid assessment finds that your workplace is required to have a level 3 first aider and a mobile treatment center, phone OH&S Safety Consulting and Training Solutions LTD. and ask us how we can help!
778-471-6407
Respirator Fit Testing
Many workers rely on respiratory protection in the form of a disposable or reusable respirator on a daily basis. But did you know, that respirators should never be the first choice of respiratory protection in workplaces?
It all comes down to what safety professionals call the hierarchy of controls. When selecting a control for a hazard we want to make sure that we our choice is guided by a rational approach that offers the greatest level of protection for workers. During my construction career, I continually saw workers, supervisors, and managers ignoring the hierarchy of controls by reaching for that respirator first. So what do we need to know about selecting hazard controls?
Engineering Controls.
The hierarchy of hazard controls tells us to first consider engineering controls to controls respiratory hazards. The most common is likely mechanical ventilation. In the photo below we can see a welder using local exhaust ventilation to remove the fume from his weld.
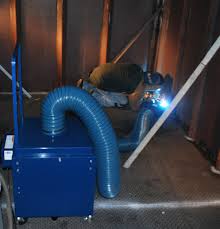
Administrative controls.
Administrative controls limit workers’ exposures by scheduling reduced work times in contaminant areas or by implementing other such work rules. These control measures have many limitations because the hazard is not removed. Administrative controls are not generally favoured because they can be difficult to implement, maintain and are not reliable. (CCOHS)
Personal Protective Equipment.
Our final choice in the hierarchy of controls is personal protective equipment; equipment such as masks, respirators, SCBA, or SABA. Relying solely on a respirator to control an atmospheric hazard is not the best way to control atmospheric hazards, however, workers are often required to wear respirators in order to provide additional protection from atmospheric hazards that have not been eliminated by the selected engineering and administrative controls.
Fit Testing.
Respiratory protection is a complex topic, and the selection and use of appropriate respirators can be challenging. Employers are required to develop a respiratory protection program designed to methodically assess respiratory hazards in the workplace and develop controls. Part of this requirement is that employers have their employees fit tested for the particular respirator they will be using.
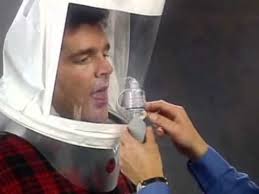
What can we do to help?
OH&S Safety Consulting and Training Solutions LTD. offers its clients qualitative fit testing for their respirators. We also sell a wide range of respiratory protection products including full and half-face masks, particulate and organic vapour cartridges, and specialty products like powered air purifying respirators, self-contained breathing apparatus (SCBA), and more.
What you need.
Simply visit us at 825 laval crescent in Kamloops, BC, or phone 778-471-6407 to book an appointment. Individuals requiring a fit test must be clean shaven where the respirator forms a seal, and must not have health concerns that might affect their ability to work safely in a respirator. We also perform fit-testing at your job site.
We have recently had the pleasure to assist the early residents of Fort Mcmurray by providing respiratory fit-testing and products. We hope that everyone reading this remembers that personal protective equipment such as respirators are our last choice in the hierarchy of respiratory protection choices. Before you reach for your mask, ask yourself if you can ventilate or implement administrative controls.
For more information visit:
https://www.ccohs.ca/oshanswers/prevention/respiratory_protection.html
http://www.ccohs.ca/oshanswers/prevention/ppe/respcare.html
Work Safe BC Information Sheet
Why have a Joint Health and Safety Committee?
In British Columbia, Joint Health and Safety Committees are required in workplaces where 20 or more employees are regularly employed or where otherwise required by order. But is the only reason to have a Joint Committee the fact that we are legally required to have one?
If that is how you feel about Joint Health and Safety Committees, it may help to learn about where they came from and why they were deemed necessary. We train a lot of Joint Health and Safety Committee members from our offices in Kamloops, and part of our training always deals with the why behind the requirements. In other words, “what got us here?” We are safety professionals after all, and a huge part of our job is to look at problems within organizational systems and ask the how and why questions.
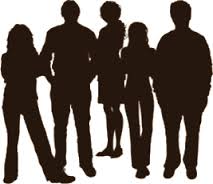
As it turns out, the why behind Joint Health and Safety Committees can be traced back to 1974 at the Elliot Lake Uranium mine in Ontario. It was there that workers went on strike over health and safety concerns arising from high incidents of lung cancer and silicosis. That’s right, in this pre-right to refuse unsafe work work-scape you had to strike in order to demand a healthy and safe work environment. The video below explains the events in 1974 well:
Since the events at Elliot Lake, the role of the Joint Health and Safety Committee has evolved and expanded. Today the duties and responsibilities for committees in BC look like this:
Identify situations that may be unhealthy or unsafe for workers and advise on effective systems for responding to those situations;
consider and expeditiously deal with complaints relating to the health and safety of workers;
consult with workers and the employer on issues related to occupational health and safety and occupational environment;
make recommendations to the employer and the workers for the improvement of the occupational health and safety and occupational environment of workers;
make recommendations to the employer on educational programs promoting the health and safety of workers and compliance with this Part and the regulations and to monitor their effectiveness;
advise the employer on programs and policies required under the regulations for the workplace and to monitor their effectiveness
advise the employer on proposed changes to the workplace, including significant proposed changes to equipment and machinery, or the work processes that may affect the health or safety of workers;
ensure that accident investigations and regular inspections are carried out;
participate in inspections and investigations;
- carry out any other duties and functions prescribed by regulation.
Joint Health and Safety Committee Training Matters!
With so many duties and responsibilities it is no wonder that Joint Health and Safety Committee member require training to do their jobs effectively. We have developed a suite of Joint Health and Safety Committee training courses to assist our clients with establishing and maintaining a truly effective JOSH Committee. We currently offer the following classes for JOSH committee members:
JOSH Committee Fundamentals; learn about:
Committee roles and responsibilities
Committee composition
Making effective recommendations
Hazard Identification; learn about:
Identification, evaluation, and control
Risk and hazard assessment processes
Unsafe act intervention
Regulatory requirements
Accident Investigations; learn about:
Accidents that must be investigated
Preliminary and full investigations
Regulatory Requirements
How to draft a accident investigation report
Safety Culture:
Current work related to safety and workplace cultures
The new view vs. the old view of organizational safety
Measuring safety culture
Positive impacts
Phone our head office at 778-471-6407 or email us at info@ohandscanada.ca for more information about our Joint Health and Safety Committee Courses.
Looking for ATV training in Kamloops? Its January 5th and all of Kamloops is covered in white stuff, people are busy snowboarding, snowmobiling, skiing, and our generally making the best of this chilly season. Soon, the snow will melt and in its wake a new batch of outdoorspeople will head to the hills. Among the hikers, mountain-bikers, horseback riders, and rock climbers, will be those who prefer to get around the backcountry at a faster clip. I’m talking about our friends, the ATV-ers.
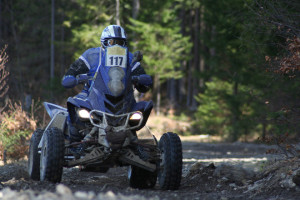
Using an All Terrain Vehicle is a great way to get outside and explore the backcountry.
Perhaps you are already gearing up for the spring season, and eyeing up your quad that has spent the long winter months inside your garage. Or maybe you are an employer whose employee’s are required to operate these machines as part of their workdays. What thought have you given to the safe operation of your machine? According to the Canadian Institute for Health Information, In Canada, the rate of ATV-related injury hospitalizations (for all ages) rose by 57% between 1996 and 2004, with absolute numbers increasing from 1700 admissions in 1996/1997 to over 2800 in 2004/2005. One possible cause for the increase in injuries is the increase in riders. There are simply more people out taking advantage of the outdoors in BC. There are also many more companies like forestry contractors, surveyors, geo-techs, and prospectors making or continuing to use ATVs a part of their vehicle fleet.
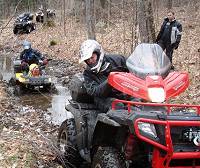
Operating an ATV requires awareness of the environment, the vehicle, and the operator’s limitations.
This Spring we are offering several one-day ATV training in Kamloops designed to boost safety awareness among ATV riders of all ages and experience levels. The background section of our ATV program provides students with knowledge of ATV ownership and registration, ATV liability insurance, ATV legislation, and the main components of the ATV.
We then provide students with information regarding the basic principles of safe operation including safe operating practices, personal protective equipment, start of shift checks, occupational concerns, and workplace hazards. From there we look at driving practice and discuss driving basics, climbing hills, and traversing slopes.
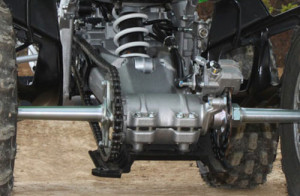
ATV maintenance like all vehicle maintenance is essential to the safe operation of ATVs.
After a discussion about operational maintenance, it is time for the class to head to the hills for some practical training. At OH&S we try to make sure that all our training contains a hefty practical component (we know how tiring it can be to sit in a classroom all day). During the practical, the instructor will guide students through the pre-operational inspection of the machine before briefing students on the terrain they will encounter and other environmental concerns that may arise. The group will then embark on the practical portion of the course where the theory the students learned in the morning will be put to the test.
We invite everyone who would be interested in attending our ATV training course to contact us at 778.471.6407. If you have any questions regarding the course or the certification you will receive, we will be happy to answer these questions for you as well.
The past year has seen our reputation grow as a high quality training center, a safety equipment retailer, and a provider of top notch occupational health and safety consulting. What was perhaps most interesting about the work we performed in the past year is how much of it was related to working in confined spaces. Throughout Kamloops and surrounding regions, clients asked for our assistance in addressing the hazards and risks of confined space work. We are quickly becoming the source for confined space consulting in Kamloops and the rest of BC. For those of you who do not know what I am referring to when I mention confined space requirements; an employer is required (by section 9.5 of the BC Occupational Health and Safety Regulations) to provide the following information:
1. An assignment of responsibilities
2. A list of each confined space or group of similar spaces and a hazard assessment of those spaces, an
3. Written safe work procedures for entry into and work in the confined space, that address, where applicable
(I) identification and entry permits,
(ii) lockout and isolation,
(iii) verification and testing,
(iv) cleaning, purging, venting or inerting,
(v) ventilation,
(vi) standby persons,
(vii) rescue,
(viii) lifelines, harnesses and lifting equipment,
(ix) personal protective equipment and other precautions, and
(x) coordination of work activities.
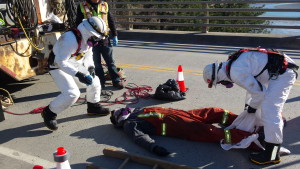
Workers perform a mock decontamination outside of a confined space.
Judging by this list of requirements, it is easy to see why employers often require some help when planning their confined space projects. We often assist clients through all the steps required to develop a confined space entry program. We will start at square one; confined space identification (which is not as easy as it sounds), develop hazard assessments that are clear and easily understandable, and then develop entry procedures that provide a detailed step-by-step account of how the confined space entry is to be performed and what controls will be required to eliminate the hazards.
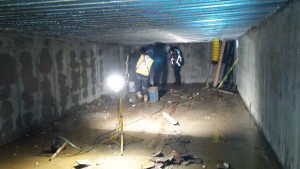
Workers finish cleaning out a water retention tank beneath a parkade project in downtown Kamloops.
What makes OH&S Safety Consulting and Training Solutions unique is the extent to which we are able to provide service to our clients. After hiring a consultant to develop the initial confined space hazard assessments and entry procedures, most employers will then need to outsource confined space entry training, standby services, lockout procedures, personal protective equipment, and sometimes standby rescue services. As a full service safety provider, OH&S can provide all of the services mentioned above in addition to professional and qualified consulting services at the outset.
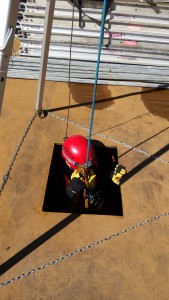
A rescue technician performing a practice descent into a barge on Williston Lake. The rescue assessments we develop are backed up by practice scenarios.
In closing I leave you with some photos taken from several projects we were involved in in 2015. Thank you to all the businesses who chose OH&S Safety Consulting and Training Solutions as your confined space entry consultant this year!
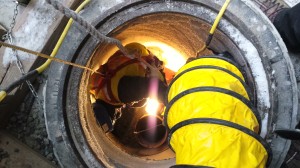
Looking down into a catch basin where a worker is cleaning debris from the basin’s inlet.
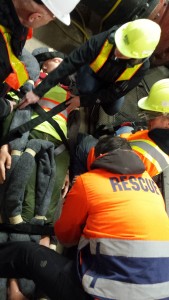
A practice scenario inside the dry well of a lift station. We wanted to be sure that the crew had the training necessary to evacuate an immobile worker from the space so we practiced with a life-sized Rescue Randy.
Click Here
With our new television commercial we wanted to demonstrate that the first aid skills taught at OH&S Safety Consulting and Training Solutions are easy for anyone to learn. We believe that the basic life-saving skills we teach will be valuable for anyone of any age!
CONFINED SPACE TRAINING
We’ve all been in one of those courses that makes you wish you were doing something more valuable with your time such as watching paint dry or banging your head against the wall. We are never surprised when we see students enter our class expecting the day to slide by slower than molasses. We see these preconceptions of confined space training as a challenge.
What is that challenge? How do we engage students in a subject that could save their lives, how do we impart our enthusiasm for workplace safety to everyone who steps foot in our building. We have never backed down from this challenge, because we know exactly how to provide engaging confined space training. The following list contains the five things that make our confined space training an excellent investment for your company.
- CURRICULUM: The curriculum is where it all starts. Basically, if we see that curriculum does not meet the needs of our students or the company who has hired us, we will not use it. We have chosen the best curriculum on the market, and to make things even better, we never shy away from injecting case studies and materials to make the subject matter more relevant to our clients’ work. After all, there is no use learning exclusively about confined space hazards on barges when you are employed at a brewery.
- INSTRUCTORS: We are proud to have some of the best instructors in the safety training industry. Our instructors have real world experience as rescue personnel, first responders, tradespeople, and more. It is this abundance of life experience that allows our instructors to relate to their students in a way that the “old boys club safety practitioner” just can’t. We always want to understand the safety issues that our students face and provide solutions for their unique needs. To do this requires great people who understand what the working world is all about.
- SIMULATORS: We don’t believe in talking for hours on end. At some point everyone needs to get out and get their hands dirty. That’s why we have built a confined space simulator that allows our students to practice the roles related to confined space entry. Training on-site? Even better, we will practice those confined space skills exactly where you will use them! Each student will get to practice being a confined space attendant and an entrant. We walk you through the permitting procedures, accountability formwork, and atmospheric monitoring. There is no doubt that our students benefit greatly from the practical portion of our confined space courses.
- CASE STUDIES: This is where the jaws drop. Most people come into a confined space course with no prior knowledge of confined space hazards. What? Most confined space fatalities involve untrained rescuers? People have died because they lack the knowledge this course provides. There is no doubt; confined space safety is no joke.
- BRINGING IT HOME: Throughout our courses we are always looking for way to maximize the impact of our material. How can we “bring it home”? To answer this we might, provide examples from our client’s workplace, ask our students to bring in examples or pictures, discuss regulatory orders, or work tirelessly in any number of ways to engage our students.
Don’t take my word for it, phone our office from anywhere at 778.471.6407, or
Stop by 825-J Laval Crescent to discuss your training needs today.
OH&S Safety Consulting and Training Solutions Ltd. Wants to Help your Business Become Heart Ready!
AED Sales and Service:
Since we started AED sales and service here at OH&S we have come to truly believe in the power of these compact and increasingly affordable devices. So much has our appreciation grown, that we often wonder why AEDs are not seen everywhere! Below you will find some information about AEDs, and if you require more information about pricing, AED training, or servicing of your AED, please phone us at: 778-471-6407.
What is an AED?
An automated external defibrillator (AED) is a portable electronic device that automatically diagnoses the life- threatening cardiac arrhythmias of ventricular fibrillation and ventricular tachycardia in a patient,[1] and is able to
treat them through defibrillation, the application of electrical therapy which stops the arrhythmia, allowing the heart to
reestablish an effective rhythm.
Some Facts:
• Cardiac arrest claims about 330,000 lives each year – or 900 per day – nationwide.
• Of approximately 10,000 people suffering a cardiac arrest each year and 95 percent of them die before reaching the hospital.
• If every community could achieve a 20 percent sudden cardiac arrest survival rate, between 45,000 and 50,000 people would be saved each year.
• For every minute a cardiac arrest victim is not defibrillated, his or her chances of survival declines 7-10%.
• About 80 percent of all sudden cardiac arrests happen at home, so being trained to perform cardiopulmonary resuscitation (CPR) can mean the difference between life and death for a loved one.
• Cardiac arrest is caused by a life-threatening abnormal heart rhythm that can result from heart attack, respiratory arrest, electrocution, drowning, choking or trauma, or it can have no known cause.
• When cardiac arrest occurs, the victim collapses and loses consciousness, stops normal breathing and loses blood pressure.
• Brain death starts to occur in just four to six minutes after someone experiences sudden cardiac arrest.
• If defibrillation can be performed within the first 1-3 minutes, there is a 70-80 % chance of survival.
• The use of effective bystander CPR nearly doubles a victim’s chance for surviving sudden cardiac arrest.
• CPR is not a substitute for defibrillation. CPR helps maintain vital blood flow to the heart and brain until defibrillation can be administered.
• Although automated external defibrillators (AEDs) were invented in the 1980s, technological advances have led to the development of more compact, portable versions.
• AEDs are safe for trained lay rescuers to treat sudden cardiac arrest because the devices automatically analyze the heart rhythm and only allow an electric shock when necessary.
AEDs are easy to use, compact, battery-operated, lightweight and durable.
The Heart Ready Vision
To Save Lives
OH&S Safety Consulting & Training Solutions Ltd. exists for the purpose of training people to save lives.
With an estimated 70,000 Heart Attacks each year in Canada alone every year, that is one heart attack every 7 minutes. The challenge is urgent and Automated External Defibrillators
(AED) technology provides a much higher survival rate. The problem? Many locations are not equipped with AEDs and people are not trained to use them. By offering easy and accessible products and training, OH&S Safety Consulting & Training Solutions Ltd. holds to its mission by seeing people more equipped to save lives in the 21st century.
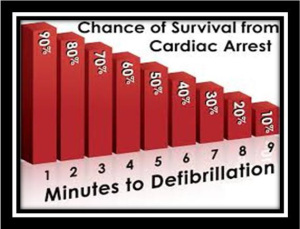
OH&S Safety Consulting & Training Solutions Ltd.,
Offers First Aid, CPR/AED training, at clients’ locations or ours. As a Philips AED Representative, we are proud to be placing one of the world’s best defibrillators into our communities.
Regular First Aid, CPR/AED Training saves lives!
Philips AED’s are one of the safest, most user friendly AED’s available and require no regular maintenance. With our “quick-shock” feature, these AED’s have the fastest CPR-to-shock sequence in the world offering BEST POSSIBLE PATIENT SURVIVAL AND RECOVERY.
PLEASE talk to us about your heart smart City, Community, Street, Hotel, Facility, Business or Home.
You’re a business owner. Which means you are also a trainer, a motivator, a salesperson, a cleaner, a labourer, a stockperson, an order taker, and order giver, a supervisor, a negotiator, and a health and safety manager… Wait? What?
That’s right, as an employer you must;
“a) ensure the health and safety of
(i) all workers working for that employer and
(ii) any other workers present at a workplace at which that employer’s work is being carried out…”
Enough has been said about due diligence and why owners and supervisors should be afraid, so I won’t spend much time beating that subject to death. Instead, I want to focus on a conversation I had with one WorkSafeBC Occupational Safety Officer regarding the topic of small business safety efforts. The following points were extracted from our conversation:
Obstacles to Small Business Safety Programs:
Larger companies can afford to hire managers for health and safety, but can Joe’s Construction Ltd? Of course not, Joe is just treading water, and he might sink if he doesn’t get paid for the last job, a safety manager is the last thing on his mind. But what if something happens to one of Joe’s workers? How will he prove that he has been duly diligent? The good news is that proving that he was duly diligent is not as expensive or arduous as Joe might think.
Lack of Training and Accountability:
If you polled your workforce and asked who of your loyal employees were supervisors; how many would you have? Would they know they were supervisors? Would they know their roles and responsibilities in regards to safety? According to the Occupational Safety Officer I spoke with, not understanding one’s responsibilities in the eyes of the Workers’ Compensation Act is a huge problem in both large and small businesses.
According to the Workers’ Compensation Act, a “supervisor” means a person who instructs, directs and controls workers in the performance of their duties;” If this describes any number of people within your company, perhaps it’s time to make it clear who your supervisors are.
Solutions:
So what can you do to overcome these obstacles? The key is in framing the problem in another way. Instead of looking at a safety program as a nebulous and vague concept that’s going to cut deeply into your bottom line ask, “what can I do today to ensure that I can prove my due diligence if needed?” According to the Occupational Safety Officer I spoke with, this is not exceedingly difficult.
Make sure your supervisors know that they are supervisors. Make sure that they understand what it means to be a supervisor; have them read part 3 of the Workers’ Compensation Act, better yet, go over it together. It is essential that these responsibilities are taken seriously and that documentation is in place to back this up.
Supervisory skills are not innately gifted onto your most experienced workers or those with the strongest work ethic. Supervisory skills are like and other set of skills. They need to be demonstrated, practiced, and honed. Supervisory training can be done through mentorships, online, or in a classroom setting. Make sure that your supervisors know how to handle key supervisory duties like disciplining, training, and journaling.
Record keeping and documentation isn’t expensive. It isn’t even time consuming. Did you have a toolbox talk? You didn’t unless you wrote it down. A well-kept journal is worth its weight in gold when a supervisor is in front of an appeal tribunal. Journals don’t need to be epic tomes, they just need to contain enough detail to say what happened and when.
Implement all of the above consistently. Hold your supervisors accountable regularly and remind them of their responsibilities. Take the time to train your workers and make sure new workers are trained the same standard. Document all of your safety efforts and document consistently.
Summary:
What we’ve discussed hear might sound familiar to some. The concept of due diligence certainly isn’t a new one, and the challenges small companies face with maintaining adequate safety programs will likely be around for a while. Just remember that in a world where business owners need to do more with less, safety cannot be thrown by the wayside. Implement the suggestions above to start and you will be on your way to building a practical small-business safety program.
Links:
http://ohandscanada.ca/
Supervisory Training
Workers’ Compensation Act: WCA
When Paul Villeneuve was 20, he was buried up to his waist in soil after heavy machinery nearby caused the trench in which he was working to collapse. Fortunately, he got out alive after his brothers, who were working on the job, dug him out with shovels.
Villeneuve of Laval, Quebec was one of the lucky ones. Had the level of soil been a bit higher, he might not have lived to tell the tale.
When you’re buried up to your chest, you’re dead. There’s too much pressure,” Villeneuve says. Some 40 years after his work accident, Villeneuve now works for ASP Construction in Montreal, which teaches compulsory courses in safety and security — including a trenching and excavation component — to construction workers in Quebec.
One of the biggest hazards of trenching and excavation work is the risk of cave-ins. Trenching fatalities are primarily caused by cave-ins, with death occurring by suffocation or crushing when a worker is buried by falling soil, notes information from the Infrastructure Health and Safety Association in Mississauga, Ontario.
Trench stability is affected by a number of factors, such as soil type, moisture content, depth of the trench, length of time during which the trench is left open, previous excavations or soil disturbances and vibration and excessive weight from heavy equipment nearby. Trench-related fatalities can also be caused by falls, exposure to hazardous gases, drowning, falling equipment or materials and electrocution.
“People think they’re invincible. They don’t realize how extremely dangerous trenches and confined spaces can be,” Villeneuve says.
An excavation is a hole made in the ground of at least four feet, with the width of its base exceeding the depth. A trench, which is also at least four feet in depth, has a base that has a width equal to or less than the depth. Several effective methods that can help prevent accidents include sloping, shoring and using trench boxes. Sloping involves cutting back the trench wall at an angle inclined away from the excavation. Shoring systems that retain the walls are usually made of wood, aluminum or steel panels held apart by shoring screws or hydraulic jacks. Trench boxes or prefabricated shoring are used more frequently to hold trench walls in place while workers are inside them.
Despite these safeguards, fatalities and injuries still occur. Last September, a worker in Westmount, Quebec was buried in a trench next to a house when the wood retaining wall collapsed on him, as did soil and paving stone. Colleagues got him out in 90 seconds, but he succumbed to his injuries shortly afterwards.
That same month, two construction workers in Toronto were pulled out alive from a collapsed trench at a house under construction. The 90-minute rescue effort involved 60 firefighters.
But a worker who was installing a sewer service in Toronto last March was not so lucky: he was killed when he fell into a trench and was buried by a concrete slab.
Shifting Ground
Most trench and excavation fatalities occur on small, short-duration jobs and involve companies with fewer than 10 employees, notes information from Ontario’s Ministry of Labour (MOL). Small-scale projects, such as excavating houses to waterproof basements, typically attract smaller companies that provide little or no training and supervision of workers, says Mike Chappell, provincial coordinator of the construction health and safety program at the labour ministry in Toronto.
“They’re hiring workers from temporary help agencies or workers who don’t have a lot of experience, and they’re loosely supervising them,” he says. Chappell reports that accidents on small jobs typically involve only a back-hoe operator and the worker in the trench. The recommended shoring or sloping protection for trenches is often not in place. Some companies take the risk that the shallow holes, which are generally two to two-and-a-half metres deep, will not collapse in the day or two during which the job is being done.
“If you’re digging in the top layer of the soil, it will stand up [for] some period of time without falling in,” Chappell says. But vibration and water destabilize the soil, and eventually, it will collapse. “It’s not a question of if, but when.”
Workers caught in that situation have very little chance to survive. “The popular belief is that if you are buried in a trench, your co-workers can jump in and somehow dig you out in time. That is not the reality,” Chappell notes. “Soil is so heavy that when it collapses, it pushes all of the air out of the lungs of a worker.” One cubic yard of soil can weigh as much as a car and the pressure on the chest can make it impossible for a worker to breathe, even if his or her head is above the level of the collapsed soil.
“You only have four, perhaps five minutes realistically to rescue a worker, and if you are covered by three or four feet of soil and try to dig that out, it’s not going to happen. It becomes a recovery situation,” he adds.
Digging Safe Workers engaged in trenching and excavation works are exposed to risks from both the top, such as cave-ins, and underground – with electrical utility services as an example. Apart from wearing the proper personal protective equipment, ensuring that workers have received proper training and making first-aid supplies available in the event of an incident, trade guidelines on excavation and trenching from the Construction Safety Association of Manitoba recommends the following safe work practices: • Do not use pointed tools to probe for underground gas and electrical services; • Protective barricades should be installed; • The spoil pile must be placed at least one metre away from the edge of the excavation, while work materials and equipment must be at least two metres back from the edge; • The trench must have adequate entrance and exit points every eight metres; • Ladders must be placed within three metres of workers, secured and capable of extending at least three rungs above ground; • If trench depth is more than one metre in height below the sloped sides, a support structure or adequate shoring must be provided; and • No vehicles should be parked within a distance equal to the depth of the excavation or they may jeopardize the stability of the walls. |
Chappell says such accidents continue to happen even though requirements for trenching and excavation safety have been in place for well over 20 years and employers are required to provide adequate training and supervision to workers.
David Law, partner at Gowling Lafleur Henderson in Ottawa and co-leader of the law firm’s national oh&s practice, says small employers who have not joined construction safety associations are more prone to unsafe practices in trenches. Even companies with adequate resources and training may have supervisors who have not bought into the safety program or may direct people to do work in a way that is unsafe, because they are under time pressure.
“A worker who knows they shouldn’t do something they think is dangerous is an employer’s best friend,” says Law, since these workers draw employers’ attention to safety concerns and bring about the opportunity to rectify them. “The missing piece, a lot of the time, is the unwillingness of individuals to say, ‘I’m not comfortable with that.’”
Horse Before Cart
A trench accident is like any other non-compliance issue, says Law, who has worked on many cases involving trenches in his 25-year career. “It’s pretty horrifying for a person to be trapped in that way, whether she lives or dies.”
Before digging even begins, On
tario’s Occupational Health and Safety Act (OHSA) requires debris and excavated soil near the excavation site to be removed. Workers must be protected from falling into an excavation and water-removal plans should be in place.
Apart from locating overhead power lines and underground infrastructure, such as gas and electric power lines, knowing the type of soil and the sloping, shoring or shielding required is critical. Having an emergency plan to deal with any unforeseen incidents is also required, notes information from the MOL.
But Chappell says Ontario does not stipulate the need for a full-time supervisor on jobs with fewer than five workers. On the other hand, “the greater the risk, the more the employer has the obligation to provide supervision.” Even for trench jobs with fewer than five workers, Chappell is of the mind that “it would be prudent to do due diligence” and provide full-time supervision.
Kimberley Labrecque, whose husband Fabien Guindon was killed by the collapse of a soil wall in Oka, Quebec in 2007 while repairing a conduit in a trench, says she continues to see trenches that are potentially dangerous. She vowed her husband’s death would not be in vain and agreed to appear in an accident prevention video for the Commission de la santé et de la sécurité du travail.
She believes that had her husband been protected by a trench box, he would not have been killed. “It’s unacceptable. Without trench boxes, trenches can become real coffins for the workers who are inside them.” Quebec’s guidelines require an experienced person who can detect faults, earth breaking or any other source of danger to be present at the ground level when employees are working in trenches.
Candice Brown, a safety and injury management advisor at the BC Construction Safety Alliance in New Westminster, British Columbia says employers planning to do trench or excavation work should call one-stop services, such as BC One Call in British Columbia and Info-Excavation in Quebec, to determine the location of underground utilities within the area. She adds that British Columbia and other provinces have the Common Ground Alliance, a non-profit organization that develops best practices and coordinates safe excavation activities near underground infrastructure.
Trench walls become less stable the longer they are exposed to rain, snow or dry weather. When trench accidents occur, firefighters are almost always called upon to rescue trapped workers. But only a minority of firefighters in Toronto have taken all three levels of trench-rescue courses available, says firefighter Geoff Boisseau, who sits on the executive of the Toronto Professional Fire Fighters’ Association. Boisseau is one of 60 firefighters who recently completed the top-tier technician level training, which deals with intersecting trenches. The first two levels — awareness and operations — deal with recognizing the general hazards associated with trench and excavation emergencies and understanding the need for protective systems to perform a safe rescue.
Silt or Sand Understanding the type of soil, which determines the strength and stability of trench walls, can help supervisors and workers plan their protection accordingly. As soil types and conditions can change over very short distances, the Construction Regulation under the Occupational Health and Safety Act sets out soil types into the following categories: Type 1: Often described as “hard ground to dig”, this type of soil, such as “hardpan”, consolidated clay and some glacial tills, is so hard that it is close to rock. Type 2: This type of soil can easily be excavated by a backhoe or it can be hand-excavated with some difficulty. The sides of a trench will remain vertical for a short period of time. Examples include silty clay and less dense tills. Type 3: This type of soil, when dry, flows through fingers and will not stand vertically. Sand, granular materials, silty or wet clays and all backfilled or previously disturbed material fall under this category. Type 4: This type of soil must be supported and contained to be excavated to any significant depth. With its high moisture content, soil of this type is very sensitive to vibration and other disturbances. Examples include muskeg, quicksand, clay and silty clay. Source: Infrastructure Health and Safety Association |
The more training firefighters have, the closer they are allowed to get to the trench during rescues, says Boisseau, who was involved in a trench rescue a few years ago. Two men were waterproofing their basement from the outside when soil collapsed and pinned them against a wall. One man was rescued, but the other had to be dug out — fortunately alive — by crews.
Boisseau says Toronto Fire Services has a specialized trench-rescue truck with the equipment required to respond to accidents, although calls for rescues of this nature are few and far between.
Employer Liability
Cheryl Edwards, partner of Heenan Blaikie and labour and employment lead at the law firm’s oh&s and workers’ compensation practice group in Toronto, points out that employers can be charged with criminal offences in addition to occupational health and safety violations in the wake of a trench accident.
For example, charges were laid against Millennium Crane Rentals of Sault Ste. Marie, Ontario in connection with a sewer work accident in 2009, when a crane that was being repositioned rolled into an excavation, killing a worker. Five charges were laid against Millennium Crane under the OHSA. The company, the crane owner and the crane operator were also charged with criminal negligence causing death.
Edwards says this was the first time a corporation in Ontario was charged with this offence since amendments had been made to the Criminal Code in 2004. While the criminal charges were withdrawn as the Crown could not prove that a lack of maintenance caused the crane to roll into the excavation, the company was fined $70,000 last July for failing to ensure that the crane was maintained in a condition that would not endanger a worker.
“There can be significant liability under occupational health and safety legislation across Canada, under the Criminal Code of Canada, for excavation-related issues to employers, to general contractors, business owners and even workers and supervisors,” Edwards cautions.
She adds the Ontario Court of Appeal ruled in September that in appropriate cases, courts can fine a company into bankruptcy for a Criminal Code conviction. In that case, the court increased the fine from $200,000 to $750,000 for Metron Corp. after the company pleaded guilty to a charge of criminal negligence causing death. The case against Metron Corp. stemmed from the deaths of four migrant workers on Christmas Eve of 2009, when the swing stage on which they were working collapsed from a high-rise building in Toronto. Edwards says higher fines are sending a message to employers that “this is not acceptable.”
Chappell notes that Ontario is working on mandatory entry-level training that will make construction workers aware that trenching and working under the soil is inherently dangerous. “Workers often have no idea. They do as they’re told. They want to keep their job and that puts them in a situation of playing the game of chance — when will this collapse? Unfortunately, they don’t know.”
Law observes that compliance with safe practices in trenching and excavation works has improved considerably over the past two decades. That said, “it shocks me to think that we have 10 fatalities a year in this country when we are equipped to deal with this.”
Danny Kucharsky is a writer in Montreal.
REGINA (The Canadian Press) — A Saskatchewan roofing company and its supervisor have pleaded guilty to occupational health and safety charges after a workplace accident that left one person with a serious leg injury.
The Ministry of Labour Relations and Workplace Safety says Clark Roofing Regina Ltd. pleaded guilty last month to two counts under provincial legislation and was fined $7,000.
The charges included failing to ensure that workers use a fall protection system, and failing to ensure that all work was sufficiently and competently supervised.
Three other counts were stayed.
The ministry also says supervisor Harold Vincent pleaded guilty and was fined $2,100 for failing to ensure that employees under his direction comply with safety regulations.
A court in Regina heard that in July, 2012, a worker fell two storeys from a roof after his leg got caught in a hoist that was being lowered over the edge.
Copyright (c) 2015 The Canadian Press
TORONTO (The Canadian Press) — A project manager who oversaw a construction crew involved in a deadly scaffolding collapse in 2009 didn’t insist workers be attached to safety lifelines and asked a survivor to lie about the incident, his trial heard Monday.
Vadim Kazenelson faces four counts of criminal negligence causing death and one count of criminal negligence causing bodily harm. He has maintained his innocence.
His judge-alone trial heard Monday from Shohruh Tojiddinov, a worker who came to Canada from Uzbekistan in May 2009 and was among a crew of migrant workers making repairs to balconies at a high-rise apartment building.
“He said ‘I don’t want to be guilty for this, responsible for this,”’ Tojiddinov recalled Kazenelson telling him in the aftermath of the incident.
Kazenelson chose to join workers who were using a swing stage to go up and down the outside of the building on Christmas Eve 2009, said Tojiddinov, who testified in Russian.
At the end of the day six workers, including the site supervisor and Tojiddinov, got onto a swing stage which only had two lifelines, the court heard.
Tojiddinov attached himself to one lifeline, as he had always done, he said.
At that point, Kazenelson was still on a 13th floor balcony beside the swing stage, handing tools to the workers on the stage.
“Do you remember him saying anything about lifelines while you were getting onto the stage?” Crown attorney Elizabeth Moore asked.
“He said ‘where is the lifeline’ and [site supervisor Fayzullo] Fazilov said ‘don’t worry,”’ Tojiddinov said through an interpreter. “He jumped into the stage…the stage broke.”
Kazenelson was still holding onto the balcony when the swing stage split in two and managed to scramble back on, Tojiddinov said.
Five others who were on the swing stage plummeted to the ground — four died and one sustained horrific injuries. Tojiddinov, who was the only one properly secured to a lifeline, was left suspended in mid-air.
“I had this harness, and I was sort of hanging in the air,” he said. “I opened my eyes and I saw birds flying and I looked up and I saw Vadim pulling me up.”
Kazenelson hauled Tojiddinov up to the balcony using the lifeline he was hanging on and then called emergency services, Tojiddinov said.
The two men then rushed down to the workers who had fallen to the ground.
“I saw four deaths and one was still alive,” Tojiddinov said, looking down at his hands as he spoke. “I vomited.”
Alesandrs Bondarevs, Aleksey Blumberg, Vladamir Korostin and site supervisor Fayzullo Fazilov fell 13 floors to their deaths. The men ranged from 25 to 40 years old and were from Lativa, Uzbekistan and Ukraine.
As police began investigating, Kazenelson instructed Tojiddinov to say he that he had been on the ground during the incident, operating a construction bucket filled with work materials that was sent up along with the swing stage, Tojiddinov said.
That bucket had been operated by a man who was not part of the regular work crew, he said, adding that Kazenelson later said the man was a relative.
The trial also heard that after the collapse, Kaznelson visited Tojiddinov at his apartment to give him a safety manual written in English, which Tojiddinov couldn’t read.
“If somebody asks about this book, then say that I received it before the accident,” Tojiddinov recalled Kaznelson saying.
Earlier Monday, the trial heard from another construction worker who was not present at the time of the incident but said he had no concerns about the safety aspects of his job.
The construction company involved in the case, Metron Construction Corp., pleaded to criminal negligence causing death and was eventually fined $750,000 plus a victim surcharge — the first time in Ontario that the Criminal Code has been used to hold a company responsible for a worker’s death.
The company that supplied the swing stage, Ottawa-based Swing N Scaff Inc., was fined $350,000 for failing to ensure the platform was in good condition.
Copyright (c) 2015 The Canadian Press
BRAMPTON, Ont. (The Canadian Press) — Two company directors have been jailed after pleading guilty to safety violations that led to the death of a warehouse worker.
Baldev Pura and Rajinder Saini — both directors of New Mex Canada Inc. — were sentenced to 25 days in jail and New Mex Canada, an importer and retailer of furniture and accessories, has been fined $250,000.
On Jan. 18, 2013, a worker was moving merchandise in a Brampton, Ont. warehouse using a combination forklift/operator-up platform called an order picker. The order picker had been modified and had an additional platform supported by the forks, which did not have a guard rail around it, and the worker wasn’t wearing fall protection or safety shoes. The worker was found on the floor and was pronounced dead of blunt force trauma to the head.
A Ministry of Labour investigation found multiple violations of Ontario’s Occupational Health and Safety Act and of Ontario Regulation 851, which covers industrial workplaces. Pura and Saini were both charged with failing as directors of New Mex Canada to take reasonable care that the corporation complied with the Occupational Health and Safety Act and with Regulation 851. In addition to the 25 days in jail — to be served on weekends — both were ordered to take a health and safety course within the next 60 days.
New Mex Canada pleaded guilty to failing to provide information, instruction and supervision to a worker regarding fall protection and/or working from a height. The company also pleaded guilty to failing as an employer to ensure the safety measures required by law were carried out.
Article Source: Copyright (c) 2015 The Canadian Press